PRODUCT INFORMATION
Factors Affecting Resin Stability IV
- front page
- product
- Water Treatment Technology
- Technology Development Department
- Factors Affecting Resin Stability IV
Product Information
- heat treatment
-
water treatment
- Arsenic remover
- Desulfurizer
- Deaerator
- Water softener (calcium and magnesium ion removal)
- Carbon filter (removes odor and residual chlorine)
- Sand filter (removal of suspended impurities)
- Iron remover (removal of iron and manganese ions)
- RO water purifier
- Pre-backwash filter
- UV ultraviolet sterilizer
- Ion exchange resin
- reverse osmosis membrane tube
- quick filter
- Various tanks for water treatment
- Various application filter media
- 美國 Clack Clark control valve
- 美國 Fleck Control Valve
- 美國 Pentair Control Valve
- 美國 Autotrol Control Valve
- Runxin Control Valve
- Injection treatment
- Technology Development Department
-
brand
- Demo brand
- US DOW
- IDEX USA
- US CLACK
- EMERSON, USA
- American PENTAIR
- SIEMENS Germany
- American PULSAFEEDER
- Denmark DANFOSS
- Thailand HAYCARB
- France SUNTEC
- UK PUROLITE
- Japanese NOP
- Japan OLYMPIA
- Japan KATSURA
- BRAHMA, Italy
- SAGINOMIYA
- HONEYWELL
- AZBIL (YAMATAKE)
- OLTREMARE
- NIPCON
- TROCHOID
- domestic
- EGO
- KATO
- LECIP
- ATS
- JACOBI
- ETATRON
- WAVE CYBER
- BOSCHINI
- NIPPON
- WL
- CASH ACME
- YAZAKI
- RUNXIN
- About | Contact
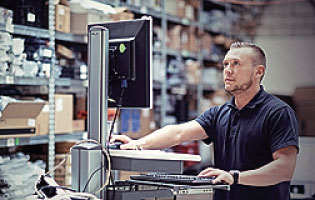
Factors Affecting Resin Stability IV
Technical explanation
The chemical and physical decay resistance of artificially synthesized ion exchange resins used in industry and commerce should be the main consideration. The cost of resin weighing needs to be reduced to achieve the highest economic efficiency. Usually the life of the resin is calculated by the number of cycles or operating years, sometimes it is expressed by the percentage of loss of operating capacity per year. The loss of resin varies with its application and the type of resin. The resin loss rate of water softening treatment is usually about 1% per year. 15 years of continuous operation without resin replacement is uncommon. In most deionization operations, the operating loss rate of cation exchange resins ranges from 5% to 25% per year. The six major factors affecting resin stability are: A) Temperature, B) Oxidation, C) Blockage, D) Osmotic vibration, E) Mechanical wear, F) Radiation.
A) Temperature:
Most manufacturers will recommend the maximum operating temperature of the ion exchanger, the maximum operating temperature of the salt cation exchange resin is between 120 and 150C and the acid cation resin is lower. The maximum operating temperature of the alkali (OH) type anion exchange resin is between 30C and 60C, while the salt type anion resin is higher. However, these maximum operating temperatures are only for reference, so the operating conditions limited to temperatures higher than 100 C do not mean that the resin will be unstable, and vice versa. The thermal decay of the resin is proportional to the temperature and operating time. Operating at the highest operating temperature does not necessarily mean that the resin will decline. Furthermore, if a short shutdown is allowed in the process to replace the resin, what's the problem with the long-term over-temperature operation?
B) Oxidation:
Ion exchange resins tend to shorten their life in strong oxidizing environments. Hydrogen peroxide, nitric acid, butyric acid and chloric acid may cause the resin to decline. Dissolved oxygen in water usually does not affect the function of the resin, but if it coexists with heavy metals, it may accelerate the resin loss (stability) under high temperature conditions, especially for anion resins. serious. Cationic resins are more stable than anionic resins. When chemical agents attack cationic resins, it will cause damage to the resin connection, increase the hygroscopicity of the resin and reduce the volume capacity of the resin. When the strong base anion resin is attacked, its polymerized part will be destroyed. However, trimethylamine can be broken or the fourth amine group can be transformed into the third amine group, resulting in the loss of the function of the resin. If the conversion rate reaches 25% or more, the drop in operating capacity (Salt Splitting Capacity) can be observed. Weak base resins with only the third amino group are more stable than strong base resins, but if the base resin is oxidized, it may turn into a weak acid resin. In this case, the resin tends to absorb sodium, so it needs to be washed with plenty of water after regeneration .
C) Blocking:
Irreversible adsorption and precipitation can cause the decline of resin function. Especially the anion exchange resin adsorbs high molecular weight organic acids, which can often cause clogging. The experience of clothing deionization treatment tells us that we should avoid clogging instead of solving this problem. Choosing the right resin can reduce clogging problems and reduce operating costs.
D) Osmotic vibration:
Alternate treatment of high-concentration and low-concentration electrolytes. Osmotic vibrations caused by resin shrinkage and expansion can lead to resin rupture. Long-term alternate operation will cause resin particle size to decrease due to rupture, resulting in pressure rise (lower flow rate) and loss of resin. This trouble can be performed between high concentration and low concentration electrolyte treatment with medium desalination osmotic shock phenomenon as follows: 4% NaOH - water - 8% H2SO4 - water. Resin particles with small particle size are generally more resistant to osmotic vibration than resins with large particle size, especially those with a particle size smaller than 0.6mm.
E) Instrument wear:
The physical stability of the resin particles is good, and they are rarely worn in normal operation, unless they are affected by external factors such as wear when changing the container, but the resin may be broken under high flow rate and the resin bed is too deep. Resin with smaller particle size is easy to wear.
F) Radiation:
Cationic resins used in such treatments usually have sufficient stability, and radiation can affect the bonding of resins. Generally, anionic resins are less stable to radiation than cationic resins, but they are also suitable for treatment under radiation conditions.